Jakarta’s rapid urbanisation is driving a booming property market replete with tall buildings which have a critical need for seismic resilience: the city is in the earthquake-prone ‘Pacific Ring of Fire’.
At 270 metres high, Menara Astra is one of the tallest in the capital. Arup’s structural and civil teams designed a well-engineered, safe, robust, durable and efficient tall building capable of withstanding a 1 in 500-year seismic event.
As the headquarters for Astra International, one of Indonesia’s largest companies, Menara Astra is a premium Grade-A commercial tower in the central business district. It houses offices, car showrooms, workshops, retail and food and beverage spaces, conference hall and a museum.
In addition to our innovative seismic design, we maximised floor space across the entire tower and expedited early completion - both of which were important to Astra International’s ongoing commercial operation.
Project Summary
2.5ha size of the development which includes Menara Astra
51storeys above ground + 6 basement levels
90%of the world’s earthquakes occur in the ‘Pacific Ring of Fire’
Safeguarding against seismic events
Some 90% of the world’s earthquakes occur in the ‘Pacific Ring of Fire’. To safeguard against these seismic events, our engineers adopted a lateral system not commonly used in Jakarta.
Drawing on Arup’s global tall buildings skill network, our design of Menara Astra’s lateral stability incorporated a dual system with a shear core wall and ductile perimeter frame, reinforced with belt trusses.
Introducing seismic separation between the tower and podium resulted in improved control over the seismic behaviour of the building. We created a clear, uninterrupted, internal space for the equipment and our belt truss solution also resolved the client’s concerns around mechanical and electrical plant space usage within the building.

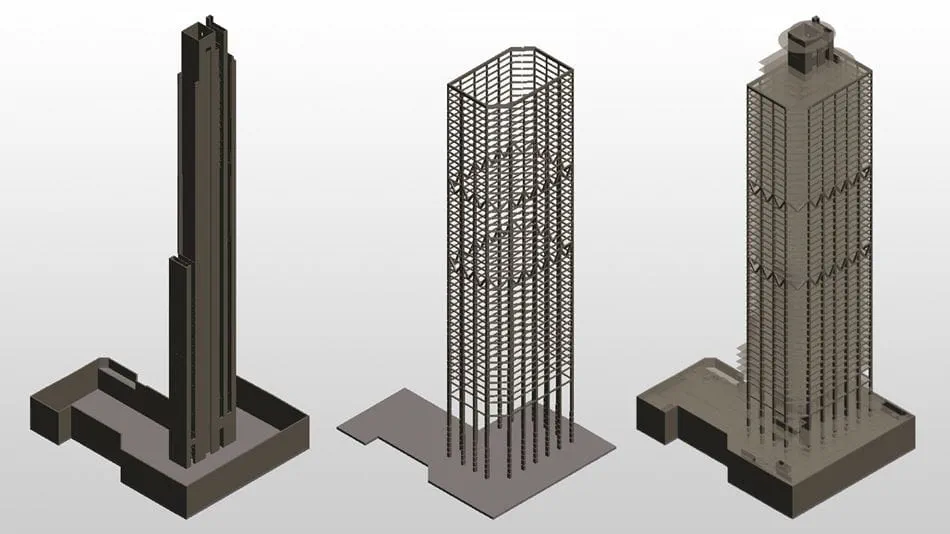
Innovation more than skin deep
Menara Astra has one of the deepest basements in Jakarta: six levels and approximately 20 metres are below ground. Our specialists proposed a semi top-down construction method for the basement. Higher level slabs with openings were constructed before excavation progressed below slab level and before casting lower level slabs.
This method minimised impact on the surrounding ground and structures, created more working space during excavation and reduced the cost of temporary works.
Future proofing was also a priority. Our team delivered a basement design incorporating knock out panels that allowed for future connection to a car park and also for pedestrian connection to the future Mass Rapid Transit station.

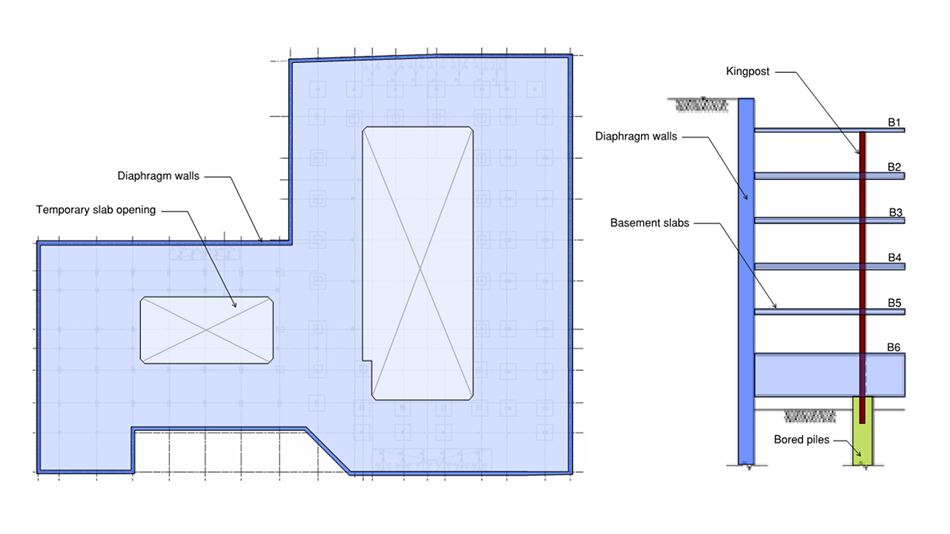


Front of mind sustainability
Our concern for sustainability was demonstrated as we minimised structures, reduced the quantity of concrete and improved the agility of the concrete used in the floor system.
Early in the project we conceived several floor structure systems, including conventional concrete beam and slab systems, concrete flat slab and flat plate design, and a steel construction with composite steel beams and decking.
© Shimizu
Our clear communication of each system’s advantages and disadvantages resulted in the client making informed and timely decisions. The benefits of the chosen conventional beam slab solution included utilising less concrete than a flat slab or flat plate system, and significant cost savings compared with the steel option.
“By adopting the semi top-down construction method and designing a diaphragm wall system with outer ring slab, we removed the unnecessary steel strappings, minimised cost and sped up construction of the basement – cutting at least three months off the overall project timeframe. ”
Rudi Lioe Project Manager
Crowning glory
As design engineer for the tower crown and annex roof, we designed the 30 metre high steel structure in tubular sections to support the façade cladding and building maintenance unit (BMU), and enabled it to brace directly to the central core for stability. The tower crown is located at level 46 and our close coordination with the façade consultant ensured we addressed the maximum permissible deformation for operation of the BMU system and we also overcame challenges such as how it interfaces with the executive floor roof slab.
© Shimizu